Алан Баликоев.
Мартенситно-стареющие стали.
Когда человек слышит слово “сталь”, то у 99% в голове всплывает “Сталь – это сплав железа с углеродом…”. На самом деле, это далеко не всегда так. Например, существует такая интересная группа сталей, как мартенситно-стареющие, которые содержат углерод лишь в качестве нежелательной примеси (существуют мартенситно-стареющие стали, в которых углерод является легирующим элементом и стали с комплексным карбидно-интерметаллидным упрочнением). Эти стали достаточно давно используются как высокопрочные и сверхпрочные конструкционные материалы, материалы для баллистической защиты и т.д. В силу совокупности эксплуатационных и технологических качеств эти стали могут быть перспективны для изготовления клинков ножей определенных классов.
Итак: мартенситно-стареющие стали. Как уже говорилось, углерода в составе нет или почти нет. И, тем не менее, отдельные представители этого класса могут иметь твердость 66-68 HRc (до 70 и несколько более). Как такое может быть? А тут принцип упрочнения зашифрован в самом названии. Мартенситно-стареющие стали (по английски – maraging steels) имеют 3 основных механизма упрочнения:
1.Твердорастворное упрочнение. Эти стали относятся к высоколегированным (зачастую суммарное содержание легирующих элементов больше 50%), поэтому вклад твердорастворного упрочнения весьма значителен.
2.Упрочнение при мартенситном превращении. Как следует из названия, стали имеют мартенситную матрицу. Правда, в отличие от “классических” сталей, мартенсит в данном случае является практически безуглеродистым и формируется вследствие легирования элементами замещении, а не внедрения (как в случае Fe-C). Такой мартенсит (фиксируемый после закалки или ТМО) имеет блочную структуру, относительно невысокую твердость (HRc 26-50) и достаточно высокую пластичность (типично порядка 60-70%), то есть весьма мало похож на мартенсит углеродистых сталей. Тем не менее, это мартенсит с высокой плотностью дефектов, что и обуславливает высокое упрочнение.
3.В процессе старения (на самом деле, с точки зрения теории термической обработки - отпуска) происходит выделение частиц (на стадии максимального упрочнения не совсем еще частиц) интерметаллидных соединений. Эти соединения образованы металлами между собой. Их тип, морфология и распределение зависят от состава стали и режима ТО, но для всех сталей есть общие закономерности: выделения имеют размеры порядка десятков ангстрем, плотность выделений высока и до определенной стадии выделения сохраняют когерентность с мартенситной матрицей. Это обуславливает очень высокое упрочнение, так прирост твердости может доходить до 35HRc против 10-12 HRc у вторично-твердеющих сталей с карбидным упрочнением.
Эти три механизма в сумме обеспечивают достижение высоких показателей прочности и твердости. В то же время, за счет пластичной матрицы (как правило – “никелевый” мартенсит) эти стали могут сохранять достаточную вязкость и пластичность. Например, “классические” стали с твердостью порядка HRc 65 имеют практически нулевую пластичность и разрушаются хрупко, а некоторые мартенситно-стареющие при той же твердости имеют относительное сужение до 20-25%.
Мартенситно-стареющие стали имеют и ряд технологических преимуществ. Например, они достаточно хорошо обрабатываются давлением и резанием в закаленном состоянии (правда, наиболее интересные нам сверхпрочные стали имеют в этом состоянии достаточно высокую твердость – HRc 33-50). Как безуглеродистые, стали практически не чувствительны к обезуглероживанию и имеют минимальные деформации при ТО.
Так что, одни плюсы? Так тоже не бывает, и у этих сталей есть свои недостатки.
1.Так как упрочняющей фазой являются мелкие и относительно мягкие (не более HV 1100) интерметаллиды, эти стали имеют относительно невысокую (для данной твердости) абразивную износостойкость. Для получения достаточно высокой стойкости РК эти стали должны иметь высокую твердость. Проблема так же может быть решена введением в состав стали твердых частиц (например, карбидов МС), не участвующих в превращениях при ТО (ТМО).
2.Из за специфики системы легирования наиболее интересные нам сверхпрочные (и, соответственно, высокотвердые) стали должны подвергаться комплексной обработке, включающей горячую деформацию по спец. режимам, закалку и старение. Это часто требует соответствующего оборудования и высокой квалификации работников.
3.Эти стали дороги и малодоступны. Собственно, стали, имеющие твердость выше HRc 60, массово не производятся.
Так где же место этим сталям, как материалу для клинков? А такие ниши есть:
1.Боевые ножи и ножи для тяжелых работ. Здесь может быть реализована высокая прочность и надежность этой группы сталей. Например, Мелита-К производит часть ножей для спецподразделений из коррозионно-стойкой стали ЭП-853.
2.Ножи, для которых важна максимальная острота РК. Благодаря сверхмалым размерам частиц упрочняющей фазы и достаточно вязкой матрице эти стали позволяют получать максимально острую РК для материалов с классической структурой. Например, из этих сталей (ЭП853, Sandvik 9RK91) производят микрохирургические инструменты.
3.Для ножей, для которых важна максимальная коррозионная стойкость (в случае применения коррозионно-стойких сталей)
Надеюсь, в ближайшем будущем мы сможем представить изделия из мартенситно-стареющих сталей с высоким комплексом свойств.
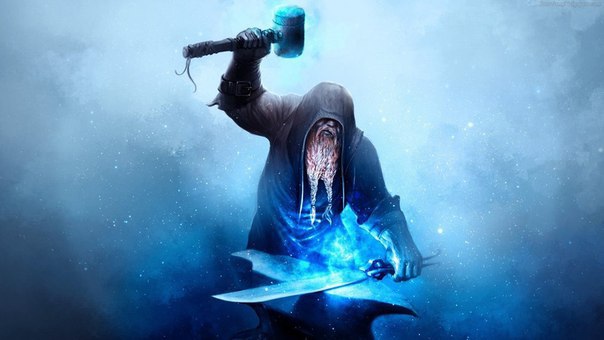